With years of experience under our belt, we possess the knowledge and expertise to tackle a wide range of plumbing issues, from minor repairs to complex installations. Whether you’re facing a broken gas line, a clogged drain, or need a sump pump installed, our dedicated plumbers are here to assist you every step of the way. We believe in delivering reliable, efficient, and cost-effective solutions that ensure your plumbing system operates flawlessly.
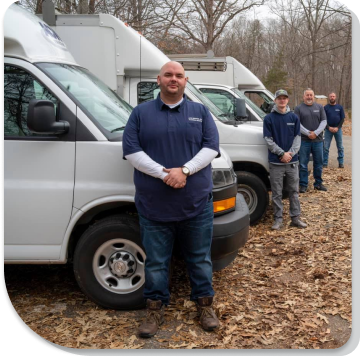
- Regular Inspections: Schedule periodic inspections by a professional plumber to identify potential problems before they escalate into emergencies.
- Maintain Drains: Avoid pouring grease, oil, or food scraps down the drains. Use drain strainers to prevent hair, soap scum, and debris from clogging the pipes.
- Watch Water Pressure: High water pressure can strain your plumbing system. Install a pressure regulator to maintain optimal pressure levels and prevent burst pipes.
- Proper Toilet Usage: Educate household members about what can and cannot be flushed down the toilet. Avoid flushing items like wipes, cotton balls, and sanitary products.
- Winter Precautions: Insulate exposed pipes, especially during freezing temperatures, to prevent them from bursting. Allow faucets to drip slowly to prevent freezing.
- Regular Maintenance: Stay on top of plumbing maintenance tasks, such as checking for leaks, inspecting pipe connections, and maintaining water heaters.
By following these preventive measures and promptly addressing any plumbing concerns, you can minimize the risk of plumbing emergencies and ensure the longevity of your plumbing system.
- Drain Snakes/Augers: Plumbers use specialized tools like drain snakes or augers to break up and remove clogs. These flexible tools are inserted into the drain and rotated to dislodge blockages, allowing water to flow freely.
- Chemical Drain Cleaners: Plumbers may also use chemical drain cleaners to dissolve or break down stubborn clogs. However, caution must be exercised as these chemicals can be harmful if not used correctly and may cause damage to the pipes.
- Video Inspection: In some cases, plumbers may perform a video inspection to identify the cause and location of a persistent drain issue. This allows them to determine the best course of action and tailor the flushing method accordingly.
Professional plumbers have the expertise and specialized tools to flush drains effectively and restore proper functionality. It’s recommended to contact a licensed plumber to handle persistent drain issues for optimal results.
- Gather Materials: You’ll need a garbage disposal unit, mounting hardware, plumber’s putty, electrical connectors, a screwdriver, a wrench, and safety gloves.
- Prepare the Sink: Start by turning off the power to the disposal unit. Disconnect the drainpipe and remove any existing hardware. Apply the plumber’s putty around the sink flange and insert it into the sink’s drain opening.
- Mount the Disposal Unit: Place the mounting ring and gasket over the sink flange and secure it with the mounting screws. Attach the disposal unit to the mounting assembly and rotate it into place.
- Connect the Plumbing: Reconnect the drainpipe using a slip nut and washer. Ensure all connections are tight and secure. Connect the electrical wires according to the manufacturer’s instructions.
- Test the Installation: Turn on the power and run water into the disposal. Check for leaks and listen for any unusual noises. Test the disposal by running it with water and some food waste.
Remember, it’s essential to follow the specific instructions provided by the manufacturer of your garbage disposal unit. If you’re unsure or uncomfortable with the installation process, it’s always best to consult a professional plumber to ensure a safe and proper installation.
- Black Iron Pipe: Black iron pipe is a popular choice for natural gas lines. It is strong, durable, and resistant to corrosion. However, its installation requires threading and sealing with pipe joint compound or Teflon tape.
- Flexible Corrugated Stainless Steel Tubing (CSST): CSST is a flexible and easy-to-install option that is commonly used for natural gas and propane lines. It allows for easy maneuverability and reduces the need for multiple fittings.
- Copper Pipe: Copper is a reliable option for gas lines, especially for propane systems. It is durable and resistant to corrosion. However, copper is not recommended for natural gas lines due to the potential for sulfur corrosion.
- Polyethylene (PE) Pipe: PE pipe is commonly used for underground gas lines. It is lightweight, flexible, and resistant to corrosion. PE pipe is typically joined using heat fusion or mechanical fittings.
It’s essential to consult with a licensed gas professional or plumber to determine the best gas line for your specific needs, ensuring compliance with local building codes and regulations.
- Plan and Prepare: Familiarize yourself with local building codes and regulations governing gas line installations. Determine the appropriate size and type of gas pipe required for your specific application.
- Shut Off Gas Supply: Before beginning any work, ensure that the gas supply to the area is shut off. This typically involves turning off the main gas valve.
- Measure and Cut: Measure and cut the gas pipe to the desired length using a pipe cutter. Ensure clean, square cuts for proper fittings and connections.
- Thread and Connect: If using threaded black iron pipe, apply pipe joint compound or Teflon tape to the threads. Use pipe wrenches to tighten the fittings securely.
- Test for Leaks: After completing the gas line installation, conduct a thorough leak test. Apply a solution of soapy water to all connections and look for bubbles. If any leaks are detected, immediately shut off the gas and rectify the issue before proceeding.
- Secure and Protect: Use appropriate clamps, straps, or hangers to secure the gas line, keeping it properly supported and protected from damage.
- Obtain Inspection and Approval: Contact the relevant local authorities to schedule an inspection of the gas line installation. It is crucial to obtain approval and ensure compliance with safety standards.
Please note that gas line installations should generally be carried out by licensed professionals experienced in handling gas systems, as working with gas can be hazardous. Always prioritize safety and consult with a qualified plumber or gas technician for proper installation.
- Visual Inspection: A thorough visual inspection is the first step in leak detection. Plumbers visually examine pipes, faucets, fixtures, and visible connections for any signs of leaks such as water stains, dampness, or corrosion.
- Water Meter Check: Plumbers may turn off all water sources in a building and monitor the water meter. If the meter continues to run or shows activity, it indicates a hidden leak.
- Pressure Testing: This method involves temporarily increasing water pressure in the plumbing system and monitoring for pressure drops. A pressure drop suggests a leak.
- Acoustic Detection: Specialized equipment, such as ultrasonic leak detectors, is used to detect sounds made by leaking water. This method is effective for identifying hidden leaks behind walls or underground.
- Dye Testing: Plumbers may introduce colored dye into toilets or drains to determine if there is a leak present. If the dye appears in another location, it indicates a leak in the plumbing system.
- Thermal Imaging: Infrared thermal cameras can detect temperature variations caused by leaking water, helping plumbers identify hidden leaks behind walls or in ceilings.
Each method has its advantages and is chosen based on the specific situation. Professional plumbers are skilled in employing these techniques to accurately detect leaks and provide appropriate solutions.
If you’re experiencing frequent leaks, water discoloration, reduced water pressure, or signs of corrosion in the pipes, it may be time to consider re-piping. Additionally, if your house has older pipes made of materials like galvanized steel or polybutylene, which are prone to deterioration, re-piping might be a wise decision.
While there is no fixed timeline for re-piping, a professional evaluation by a licensed plumber can help determine the condition of your pipes and recommend the appropriate course of action. It’s also beneficial to be proactive and schedule regular inspections to identify potential issues before they escalate.
The decision to re-pipe a house depends on the specific circumstances and expert advice. Consulting a plumber is crucial in assessing the condition of your plumbing system and determining if re-piping is necessary.
Regular maintenance plays a crucial role in extending the life of an ejector pump. It is recommended to adhere to the manufacturer’s guidelines for maintenance, which may include periodic cleaning, checking the float switch, and inspecting the pump for any signs of wear or damage.
The workload the ejector pump handles can also impact its lifespan. If the pump is subjected to heavy usage or frequently deals with solid waste, its longevity may be reduced.
It’s important to monitor the performance of the ejector pump regularly. If you notice any unusual noises, frequent clogs, or inconsistent operation, it may indicate a problem with the pump that requires immediate attention.
Proper maintenance, regular inspections, and addressing issues promptly can help maximize the lifespan of an ejector pump and ensure its reliable operation.
- Persistent Blockages: If multiple drains in your home, such as sinks, toilets, or showers, are frequently clogged despite attempts to clear them, it may be a sign of a collapsed sewer line obstructing proper flow.
- Foul Odors: A strong, persistent sewage smell emanating from drains, the yard, or the basement could indicate a sewer line problem, including a collapse.
- Slow Drainage: If water is slow to drain from multiple fixtures or if you notice gurgling sounds coming from drains, it could be due to a collapsed sewer line impeding proper flow.
- Wet Spots or Sinkholes: A collapsed sewer line can cause water to accumulate in the yard, leading to wet spots or even sinkholes developing.
- Sewage Backup: The most severe indicator of a collapsed sewer line is raw sewage backing up into toilets, sinks, or drains. This requires immediate attention from a professional plumber.
If you suspect a collapsed sewer line based on these signs, it is crucial to contact a licensed plumber who can conduct a thorough inspection and determine the extent of the issue. Timely intervention can prevent further damage and facilitate the necessary repairs.
The feasibility of tying into an existing sewer line depends on factors such as the capacity of the sewer line, its material, and its condition. Additionally, obtaining the necessary permits and adhering to specific guidelines may be required.
Professional plumbers use various methods to tie into an existing sewer line, such as using a tee or a wye fitting, depending on the configuration and accessibility of the existing line. The process typically involves cutting into the existing line, creating a connection point, and securely joining the new line.
It is crucial to have the work performed by a qualified plumber to ensure that the tie-in is done correctly, minimizing the risk of leaks, blockages, or damage to the existing sewer line.
- Waterproofing Membrane: Applying a waterproofing membrane, such as a liquid or sheet membrane, is crucial to create a barrier that prevents water from penetrating the wall. This helps protect the underlying structure from moisture damage.
- Cement Backer Board: A Cement backer board is a popular choice for providing a stable and moisture-resistant surface behind the shower surround. It is durable, resistant to mold and mildew, and can be installed directly on the wall studs.
- Greenboard or Moisture-Resistant Drywall: Greenboard or moisture-resistant drywall can be used in areas that do not have direct exposure to water. They are treated to resist moisture to some extent and are commonly used in non-wet areas of the bathroom.
It’s important to follow the manufacturer’s instructions and local building codes when selecting and installing the materials behind a shower surround. Consulting a professional contractor or plumber can ensure that the proper materials and techniques are used for a reliable and water-resistant installation.
- Water Meter Test: Turn off all water sources in your home and monitor the water meter. If the meter continues to show water usage, it indicates a leak, but it may not pinpoint the exact location.
- Visual Inspection: Look for signs of water damage, such as damp spots, discoloration, or mold growth on walls or floors near the slab. These visual cues can provide hints about the general area of the leak.
- Acoustic Listening Devices: Professional plumbers may use specialized listening devices to detect the sound of water escaping under the slab. These devices can help pinpoint the location of the leak.
- Thermal Imaging: Infrared cameras can detect temperature variations caused by the presence of water. By scanning the concrete slab, areas with abnormal temperature patterns can indicate the location of a leak.
- Slab Penetration: In some cases, it may be necessary to create small access points in the slab to visually inspect and confirm the location of the leak.
It is important to consult with a professional plumber experienced in leak detection under slabs. They have the expertise and specialized equipment to accurately locate and repair water leaks, minimizing damage to your property.
- Collection of Water: Water from the surrounding area or the drainage system is directed into the sump pit, which is a hole or basin in the lowest part of the area prone to flooding.
- Activation: When the water level in the sump pit rises to a certain predetermined level, a float or sensor triggers the sump pump to activate.
- Pumping Action: The sump pump uses an impeller or motor to pump water out of the sump pit. It moves the water through a discharge pipe or hose and away from the building’s foundation or into a designated drainage area.
- Prevention of Flooding: By efficiently removing water from the sump pit, the sump pump helps prevent flooding, water damage, and potential structural issues.
Sump pumps are particularly beneficial in areas with high water tables, heavy rainfall, or properties susceptible to basement flooding. Regular maintenance and testing are important to ensure the sump pump is functioning properly when needed.
Tankless water heaters are more energy-efficient because they heat water only when it is needed, eliminating the standby energy losses associated with keeping a tank of water constantly heated. This efficiency can result in reduced energy consumption and lower utility bills.
Estimates suggest that operating a tankless water heater can be 10% to 20% more energy-efficient compared to a tank-style water heater. However, it’s important to note that the upfront cost of a tankless water heater is typically higher, which can impact the overall cost savings.
To get a more accurate idea of the potential savings, it’s recommended to consider factors such as the local energy rates, household hot water usage patterns, and the specific efficiency ratings of the tankless water heater being considered. Consulting with a professional plumber or conducting a cost analysis can help determine the potential cost savings specific to your situation.
- Age: The age of the water heater is a crucial factor. Most traditional tank-style water heaters have a lifespan of around 8 to 12 years. If your water heater is approaching or surpassing this age range, it is more prone to developing issues and may be due for replacement.
- Rust and Corrosion: If you notice rust or corrosion on the tank or water connections, it can indicate that the tank is deteriorating and may soon develop leaks.
- Water Leaks: Leaks around the tank or from the pressure relief valve suggest a failing water heater that may require replacement. Significant leaks can cause water damage and should be addressed immediately.
- Inadequate Hot Water: If your hot water supply has become consistently insufficient for your needs, even after adjusting the thermostat, it may be a sign that the water heater is no longer functioning properly.
- Strange Noises: Excessive popping, rumbling, or banging noises coming from the water heater during operation can indicate sediment buildup or other internal issues, which may necessitate replacement.
- Decreased Efficiency: A sudden increase in energy bills or a noticeable decline in the water heater’s efficiency can indicate that the unit is no longer operating optimally and may need replacement.
It is important to consult with a licensed plumber to assess the condition of your water heater and determine if replacement is necessary. A professional can provide expert advice and guidance based on the specific circumstances and condition of your water heater.
